The risks and rewards of reshoring
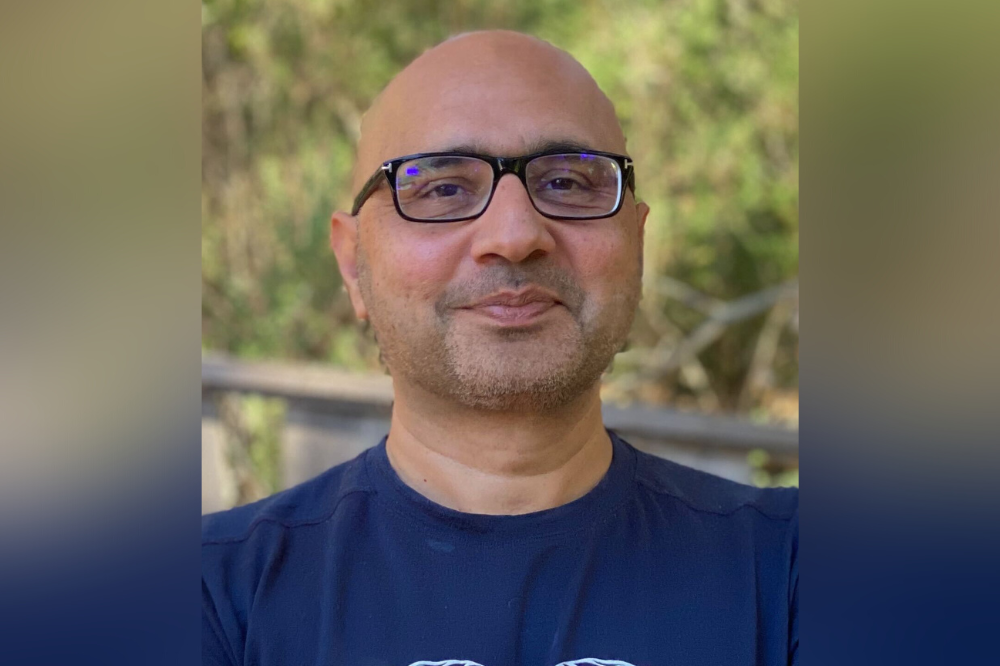
Offshoring, commonly defined as relocating of a business process from a company’s home jurisdiction to another, began growing in popularity in the 1980s, with US and other Western companies moving their manufacturing activities to countries with lower costs of labor and other inputs.
However, the opposite process, known as reshoring, has been gaining traction in recent years, spurred by the supply chain disruptions caused by the COVID-19 pandemic, critical failures such as the Suez Canal blockage, and geopolitical conflicts, such as the Russia-Ukraine war.
Jag Lamba (pictured above), CEO of third-party risk management (TPRM) firm Certa, spoke with Corporate Risk and Insurance about the various risks and rewards businesses face when reshoring their production capabilities.
“An extreme level of instability and disruption to normal supply chain activities has characterized the last few years across the globe,” Lamba said. “Even in countries where companies typically outsource their production activities because of high levels of stability, these disruptions are taking their toll. The pandemic, increased geopolitical tensions, trade wars and tariffs, and climate change (as well as rapidly changing regulations to help combat it) all impact the supply chain and make it more difficult for companies to meet their deadlines and consumer demand.”
According to Lamba, missing deadlines and customer expectations due to supply chain interruptions can be devastating for businesses, which is why many firms do not want to take that risk.
“With facilities physically distant and a number of other aspects of production (like output, timeliness, and quality) out of the company’s full control when in another country, many are reshoring to keep a closer eye on the situation,” he said. “With even usually politically stable countries feeling a lot less calm in recent years, it feels like there’s more risk than ever out there.”
Lamba said that resilient supply chains are a fundamental part, not only of a single company’s success, but also of overall national security and economic prosperity.
“A Kearney report found that nearly four out of five executives (79%) have either already transferred a portion of their Chinese manufacturing to the United States or have plans to do so in the next three years, and another 15% are considering similar moves,” Lamba said.
Major risks of reshoring
According to Lamba, there are two major risks involved with moving back production to Western shores – increased costs and timeline disruption. Companies should anticipate plenty of both before making any major moves out of any country.
“First off, the US tends to have higher production costs than many countries commonly used for outsourcing – that’s the whole reason companies set up out there – so operations locally will simply cost more than keeping them abroad,” Lamba said. “Whether those increased costs are worth the reduction in risk is up to a company’s risk appetite and the calculus for that move, which needs to account for a myriad of factors like price differential, the impact a slowdown or shutdown abroad would have on the company, public perception of the move, and so on. Oftentimes, when you see a move back to the US go awry, it’s because there was a miscalculation brought on by overlooking something big like this.”
Lamba said that companies should always take time when assessing new suppliers to properly assess each one, as sourcing and onboarding new suppliers comes with a host of security, data, and compliance risks.
“Another mistake we see companies make is not adequately screening sub-suppliers – that is, the suppliers’ suppliers – to assess the associated risks,” he said.
Mitigating reshoring risks
TPRM technology can help companies proactively identify and avoid the risks involved in reshoring businesses.
“A leading platform in the space like Certa can provide comprehensive risk scores on current and potential vendors and automatically identify risks not just when a supplier comes on board, but also on an ongoing basis.” Lamba said. “These due diligence checks are powered by data that provides risk coverage in the areas of information security, privacy, compliance, resiliency, economic sanctions and more. Moving production from one country halfway across the world back to the US is something that inherently has a fair amount of risk. But having transparency into those risks and a clear path to prevent or address them is extremely powerful.”
A powerful tool is worthless if it can’t be used, so Lamba said that the Certa platform was designed to be easy to learn and use without sacrificing capability.
“There’s no coding required; the drag-and-drop system allows procurement and risk professionals to quickly adapt their supplier management processes to whatever the situation may be without needing the IT team to get involved,” he said. “And with timelines being dragged down in major moves like these, workflow automation features are crucial to getting new suppliers up and running quickly and keeping disruptions to a minimum. A platform like Certa’s with the capability for parallel approvals, integrations with over a hundred enterprise and best-in-class data systems, and risk assessments that stretch across domains like privacy, compliance, and information security, is a must for companies looking to reshore.”
The future reshoring landscape
Lamba cited a report by Goldman Sachs which showed that US stocks of companies connected to reshoring have been outperforming those linked to offshoring activities. This, he said, suggests that the market is confident in reshoring as an effective strategy in the medium to long term, outweighing the immediate inflation-driven cost increases of reshoring.
“I expect to see selective reshoring continue for the foreseeable future.” Lamba said. “It won’t be an all-or-nothing proposition. Firms will be taking steps to build resilience into their supply chain and ensure that every part of that chain has adequate plans in place to cope with global crisis or disruption. In some cases, that means creating the capacity for a reserve supply in the US to mitigate the risk of shipments being delayed from overseas. Others may look to spread out their risk by multi-sourcing: managing parallel supply chains, with one item of supply coming from multiple sources. In that situation, it makes sense not to bring all manufacturing back to domestic shores; having operations in multiple regions mitigates the impact if one region were to fall into crisis.”