Preventing water damage during construction
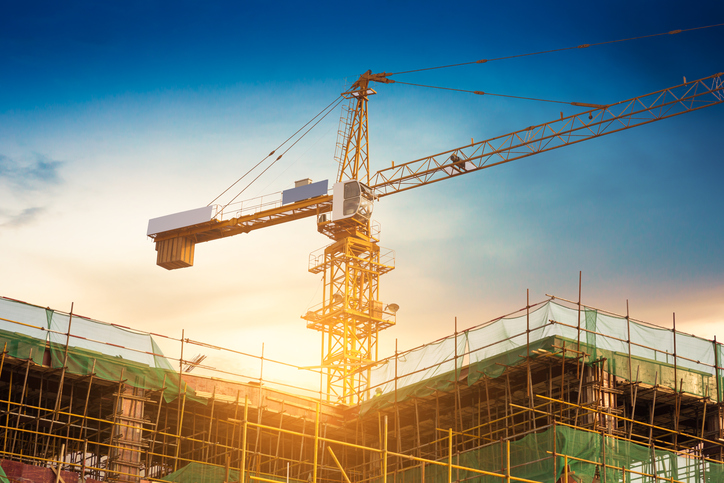
Authored by QBE Senior Risk Manager Ryan Jones
Water damage is one of the most frequent and most costly causes of insurance claims in the UK construction industry.
The number one cause of large loss suffered by QBE construction customers is fire – but water damage isn’t far behind.
Escaping water isn’t a new problem, though the severity of water damage losses has been steadily increasing, pushed up by the increased value of commercial property per square foot, the growing prevalence of high-rise buildings, and rising construction industry and supply chain costs.
In recent years, the construction industry has experienced some of the largest ever water damage insurance claims. For example, water escaping from a failed joint at a high-rise development in London recently led to a £25 million insurance settlement.
Typical incident
Based on our experience as one of the leading insurers to the construction industry, incidents typically involve the following factors:
Connection / joint failures in water systems are the main cause of large loss. Mechanical joints such as pressed fittings and compression joints bring an increased risk of defect-related loss as it can be difficult to identify problems with installation.Mechanical joints are more likely to fail than traditional soldered joints.Older buildings undergoing refurbishment present a higher risk than new build projects.Many large losses are associated with multi-storey buildings and hospitals.Around two-thirds of large water damage incidents occur outside normal working hours. Water can be running throughout the building before being discovered.Typically between one and six storeys are impacted.
Joint failures are the main cause of large water damage losses, followed by pipes and outlets having been accidentally left open. Together, these account for around three-quarters of QBE water damage claims. With as many as 1,500 mechanical joints typically found in just one floor of a high-rise building, a defect or failed joint can cause a large loss if not quickly discovered. Examples:
A ball-valve compression joint failed in a top floor plant room of a four-storey office block, just a few weeks from handover to the client. The incident occurred one week after the mains water was connected but several months after the valve had been tested and put into service, causing significant damage and a five-month delay to project completion.
A large escape of water during testing caused extensive damage during the construction of a multi-storey state of the art hospital block, just days before the project was due to be handed over to the client. An obstructed shower waste caused water to overflow undetected for 10 hours, resulting in significant damage to the building and operating theatres and a six-month delay in completion.
Loss prevention
Successful management of water on a construction site should form a prominent part of the project risk register.
There should be a formal water management policy and system that is applied to all projects in the same way as a system for managing health and safety risks on site. The policy should give clear roles and responsibilities for actions to prevent water damage incidents. The management system should include procedures for risk assessment, incident investigation, vetting contractors, expected standards for monitoring water flow and isolating systems, a quality control plan including water system testing and commissioning and auditing of compliance with local regulations and the company’s specified management system.
As part of the management process a detailed risk assessment should be carried out to identify potential water damage issues and should include consideration of:
Permanent internal systems containing water, e.g. plumbing, drainage and fire protection.Timescales for the building being weathertight in relation to the internal works commencing and water sensitive material being installed.Temporary water supplies in place specifically for the duration of the project.Water proofing and damp proofing activities.External water sources, such as rain, sleet, snow entering the building during construction.The potential for cracks and deficiencies in roofs, doors, windows, rooftop water tanks and walls and waterproof structures.Any previous loss history involving water damage relating to the site.The susceptibility of building materials and fittings to water damage and necessary delivery and storage arrangements.The effect of construction defects, such as flashing, window installation, etc.Groundwater level and nearby watercourses.Potential for flooding of excavations.
Best practice
At QBE, we are working to promote higher standards of loss prevention for water damage. Our in-house Risk Solutions team is engaging regularly with customers to provide risk management advice and feedback on our claims experience.
We also advocate best practice, most notably the Construction Insurance Risk Engineers Group (CIREG) Best Practice Guidance: Managing Escape of Water Risk on Construction Sites – available here.
Water damage risks should take a prominent place in the project risk register, with the principal contractor taking overall responsibility for the management of water damage risk. In particular, the CIREG best practice calls for a formal Water Management Plan to address the management, prevention and mitigation of risks associated with permanent and temporary water systems, as well as those dealing with rain, storm, flood and groundwater. A sample template for this is included within the CIREG document.
There’s also greater emphasis on water management isolation procedures and leak detection devices. The guidance recommends installing leak detection systems with audible alarms and / or linked to remote monitoring when the building is left unattended.
We have a free QBE Construction whitepaper on water damage which you may find useful to use alongside the CIREG Best Practice Guidance.
QBE Contractors Combined insurance
Every project can be different, so contractors need to be open-minded, agile and adaptable. That’s why we have the insurance to match. Our new Contractors Combined packages the main insurance covers into a single policy to meet the specific needs of the mid-market contracting sector.
Customers can also access a library of Risk Snapshot guides, guidance notes, toolkits and other risk management material, along with RoSPA accredited online health and safety e-learning.
You can find out more about QBE Contractors Combined insurance here.
Downloads