Managing airborne hazardous risks
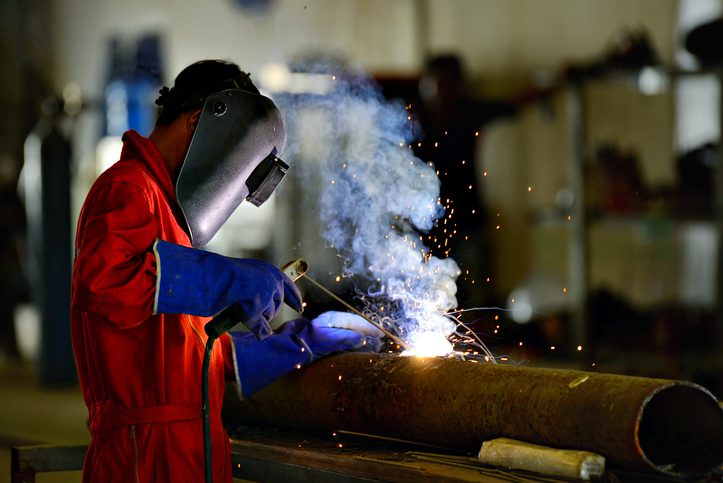
Authored by HSB
It can be surprising just how many industries employ local exhaust ventilation (LEV) for their operations. Used to prevent or reduce the level of airborne hazardous substances being inhaled by people in the workplace (e.g. fumes, vapours, gases, dust), LEV can be found in all sorts of locations.
From the more obvious industries such as construction/building contractors (i.e. welding fumes), chemical processing businesses and catering kitchens, through to less obvious locations like bakeries (flour dust, which can become explosive), ice rinks (skate sharpening) and even chiropodists/podiatrists (microbial dust).
Under the Control of Substances Hazardous to Health Regulations 2002 (COSHH), employers/duty holders are required to assess the risk to the health of employees associated with exposure to hazardous substances.
COSHH covers many aspects of safe management of hazardous substances, including risk assessment, control measures, inspection and testing, maintenance, and training. Employers/duty holders must ensure that any exposure is prevented, or adequately controlled, with control measures (e.g. LEV).
Health and Safety Executive targets fabricated metal businesses
As reported in our technical bulletin ‘Welding fume safety alert: Change in enforcement for mild steel welding fume’, during February 2019 the Health and Safety Executive (HSE) strengthened their enforcement expectation following updated scientific evidence regarding the effects of welding fume on human health (HSE safety alert: STSU1 – 2019). Processes such as welding and machining with metalworking fluid have been proven to contribute to lung cancers, asthma and many other serious health conditions.
During spring 2021, HSE wrote to fabricated metal businesses across Great Britain to check that they are complying with guidance to manage the risk of respiratory diseases; specifically, welding fume and metalworking fluid risks. Throughout the summer of 2021, HSE inspectors will be visiting those businesses to ensure employers/duty holders understand the risks, plan their work, and have adequate control measures in place to protect employee health.
It is essential that the risks from these processes are fully understood, suitable and sufficient risk assessments are developed and maintained, with appropriate control measures employed (where necessary) and suitably maintained (e.g. LEV coupled with Respiratory Protective Equipment (RPE).
Where control measures include LEV, then there is a duty to have these systems periodically thoroughly examined and tested at specified intervals (Regulation 9, COSHH). This is where inspection service providers, like HSB, can provide support with these types of periodic thorough examination and testing to assist in compliance with health and safety requirements.
HSB Inspection Services
Our inspection services can assist in compliance with health and safety legislation, provided in the role of ‘Competent Person’. Carried out by our network of competent, technically-experienced Engineer Surveyors across the UK and Ireland, we can provide periodic thorough examination and testing of LEV systems with regard to Regulation 9 of COSHH, based on commissioning or manufacture specifications provided.
To find out more, CLICK HERE