Loss Control Tips: General Contractors
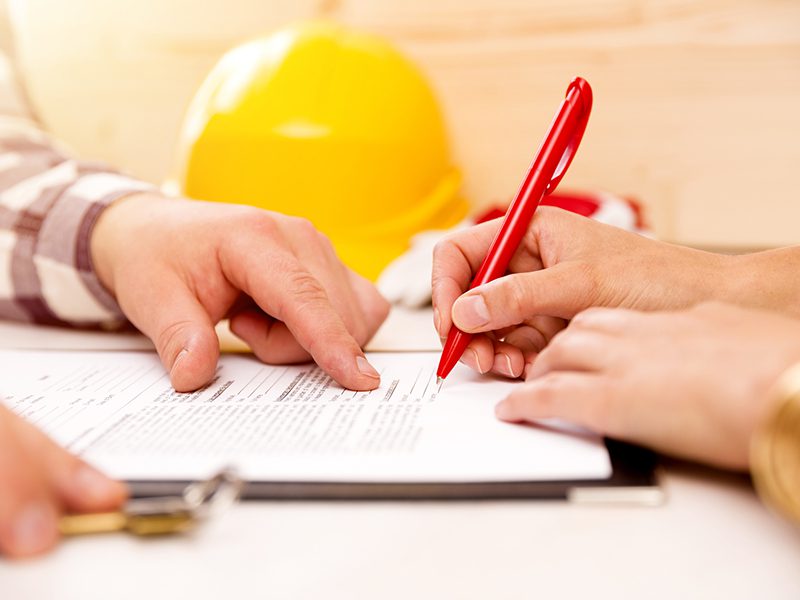
General contractors coordinate and manage all materials, activities and personnel involved in both residential and commercial construction projects. Their duties often involve hiring and training subcontractors, applying for necessary licenses and building permits and providing hands-on supervision and guidance to workers on the job site. Due to their wide variety of operations and responsibilities, these professionals are often exposed to many safety, liability and property risks. That’s why it’s vital to have effective loss control measures in place. This resource outlines common risks general contractors must address, and offers helpful strategies to avoid possible claims.
General Contractors: Premises & Operations Liability
The nature of general contracting operations poses various liability concerns. For example, third-party property damage and injuries can lead to costly liability claims. Excavation operations can also cause drainage and erosion problems, undermine the foundations and structural integrity of other properties, and affect gas and electrical lines. Therefore, it’s important for general contractors to take the following measures to limit their premises and operations liability:
Create a housekeeping program to make sure materials, tools and other objects are secured to prevent them from falling. This program should also address slips, trips and falls by ensuring spills are cleaned up promptly and all areas are kept free of debris.
Ensure there is a fire protection plan in place and that it is communicated to each employee. If smoking is allowed on the job site, create a designated smoking section.
Develop and implement a trenching safety program, including posting signage to signal there is open trenching and making sure shoring, sloping and shielding are used appropriately. It’s also important to make sure grading and soil compaction are done properly.
Ensure site security measures—such as fences or security personnel—to prevent the general public from trespassing on job sites..
Develop and implement policies and procedures for entering residents’ homes to prevent property damage.
Ensure there is a hot work program in place. Keep fire extinguishers near any area in which hot work is being performed and make sure all employees are trained on how to use them.
Employee Safety
As an employer, general contractors must protect their employees from illnesses and injuries on the job. Occupational risks related to general contracting include significant exposure to falls, back and struck-by injuries, and slips, trips and falls to name a few. General contractors should implement these employee safety precautions:
Establish a fall protection program and train employees on how to properly use fall protection.
Implement a ladder safety program and ensure employees have been appropriately trained in ladder safety.
Create a slip, trip and fall program. Perform slip, trip and fall assessments to determine the likelihood of such an accident occurring on the job site.
Ensure employees receive sufficient training before using tools or equipment.
Create an incident investigation program that allows for swift and thorough incident investigations to take place.
Establish a personal protective equipment (PPE) program and perform a PPE survey to determine what is needed for each task. Provide all necessary PPE to employees and educate them on the proper use of this equipment.
Identify a competent person on the crew to whom employees can report to. The competent person should also conduct regular trenching and excavation inspections to ensure proper safety prevention techniques are being used.
Train employees on how to use excavation and trenching equipment, as well as how to properly dig trenches and perform excavations. Ensure operators have been properly trained through school or other programs.
Inland Marine—Equipment
General contractors face many inland marine exposures, especially since they often use their own construction equipment and tools at job sites. Inadequate maintenance procedures and a lack of prevention protocols can result in equipment damage, which could lead to significant interruptions and costly repair or replacement expenses. General contractors should consider these steps to limit risks:
Keep a detailed list of machinery and tools. Each item should include an identifying number, age, type and condition. Never leave tools on-site or out in the open. Either put them in a vehicle or have a secure place to store them.
Add nonremovable labels to equipment to allow for easy and permanent identification.
Implement security measures to prevent equipment left at job sites from being damaged, vandalized or used by unauthorized parties. These measures can include installing security cameras, locking equipment doors and hiring on-site security.
Create a program requiring inspections on equipment prior to use. Corded tools should be inspected to make sure there are no cuts or frayed wires.
Automobile Liability
Because general contractors often have their own fleet of vehicles and employees frequently travel between different job sites, commercial auto exposures are substantial. In particular, accidents on the road could result in serious ramifications, including employee injuries, costly property damage and potential liability issues involving pedestrians or other motorists. To minimize commercial auto exposures, general contractors should follow these protocols:
Make sure all drivers possess acceptable driving records. Specifically, it’s important to secure motor vehicle records (MVRs) for all drivers. MVRs should be updated annually.
Provide employees will proper training on safe driving measures. Be sure to prioritize loading procedures so employees load vehicles appropriately.
Prohibit employees from using their cellphones while driving.
Consider utilizing telematics technology within commercial vehicles to identify employees’ risky driving behaviors (e.g., speeding and hard braking).
Implement an effective vehicle inspection and maintenance program. Such a program can help ensure all commercial vehicles remain in good condition and are safe to operate.
Review all commercial vehicle and trailer characteristics (e.g., size and weight) to determine applicable Federal Motor Carrier Safety Administration (FMCSA) regulations. Routinely monitor compliance with FMCSA standards and make operational adjustments as needed.
We can help General Contractors
It’s essential for general contractors to implement proper risk management precautions to limit costly insurance claims and lawsuits. Doing so can offer various benefits, such as greater customer satisfaction, bolstered employee safety, fewer liability concerns and reduced potential for property damage.
Although this resource provides a range of loss control strategies, general contractors don’t have to establish their risk management programs alone. Working with a qualified and experienced insurance professional can make all the difference.
We know the industry, we understand your needs, and we work with multiple insurance companies so we can deliver the insurance solution that’s perfect for your business, and your budget.
When you have confidence in your business insurance, you have greater peace of mind knowing that you can keep working to generate revenue, even when disaster strikes.
To get started on your customized solution, contact one of our Licensed Advisors, or Request a Proposal and we’ll get to work right away.