How brokers can help clients nip construction defects in the bud
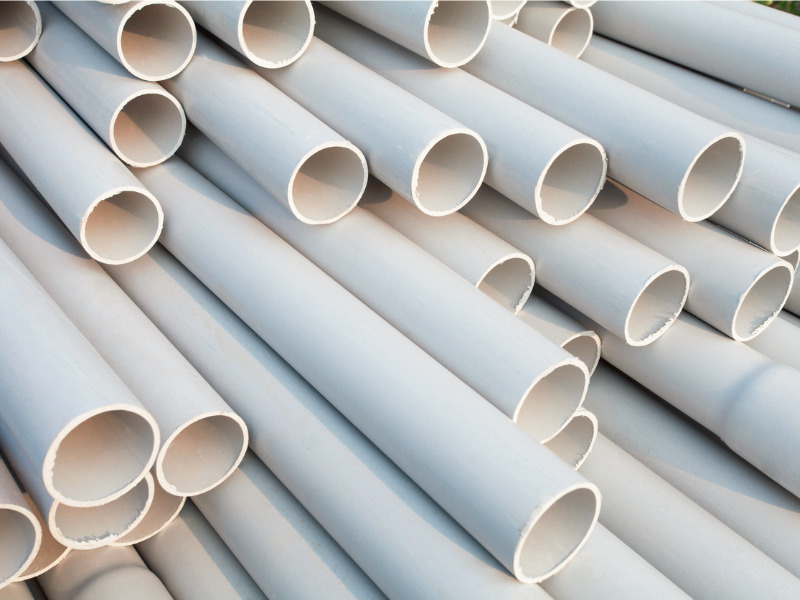
Understanding proper storage and handling of materials can help your construction clients avoid a loss later down the road.
Being able to identify material damaged by ultraviolet rays or weather is a key component of a construction risk management plan, says Paul Gallately, assistant vice president of risk control with Travelers Canada. This construction defect exposure can ultimately cause damage in the future, although it may not necessarily be realized right away.
“[Certain] materials may become subject to weather-related damage or even traditional loss like fire or water damage if you store them offsite or on-site,” Gallately says, using drywall or plastic piping as examples. “If you need to try and replace material because the material may not be available, make sure that you’re working with the manufacturer or fully understand the material that you’re replacing it with, and also that you’re not using something that may be inferior or not appropriate for what you’re trying to replace.”
Identifying this risk in the pre-planning process is ideal.
“It really comes down to due diligence and control visibility into the material being used,” Gallately says. “Documentation is incredibly important. Make sure you have proper procedures in place to [note] any changes in the order, sign-off approval, anything related to the project, for as long as possible, just to be able to address and construction defect issues that come up post-project.”
Lanny Hoang, managing director of oil and gas with Travelers Canada, says construction defect exposure is common. It could be caused by miscommunication, or perhaps contractors, labourers or other parties have not understood the proper storage and handling of materials. “It’s really just around underestimating the extent of damage that can happen from improper material storage or usage.”
Gallately and Hoang encourage contractors to work closely with brokers, who can provide the knowledge and experience in the industry to support clients’ needs.
Another important factor to consider revolves around relatively new construction methodologies or techniques. For example, use of timber-based construction and cross-laminated timber has increased, Gallately says.
Changes introduced to deal with the effects of climate change or energy efficiency are also gaining steam. “From our perspective, there are several questions around new construction methodology,” Gallately says. He notes the latest version of the National Building Code of Canada has been delayed, but changes will revolve around more energy efficient construction.
New technology is also making its way onto a project site. “We see advanced camera systems, automated machinery, project management software usage and virtual documentation,” Hoang says. “They’re very beneficial to how you run and manage a project. But then of course there’s increased risk of cyberattacks… [and] any downtime.”
With all these changes, tradespeople are having to pivot and learn or enter new areas of construction they may not have experienced before. It’s incredibly important to understand the contracts (standard or revised) that contractors, subcontractors, and vendors have signed, Gallately says.
“It’s just making sure that you have a full risk management plan in place,” he says. “Make sure that you have a proper program in place so that if there is a lack of experience or training in any one area, then you have the ability to support [these workers].”
Feature image by iStock.com/koosen