Automakers are replacing decades of know-how with strategies from Tesla's playbook
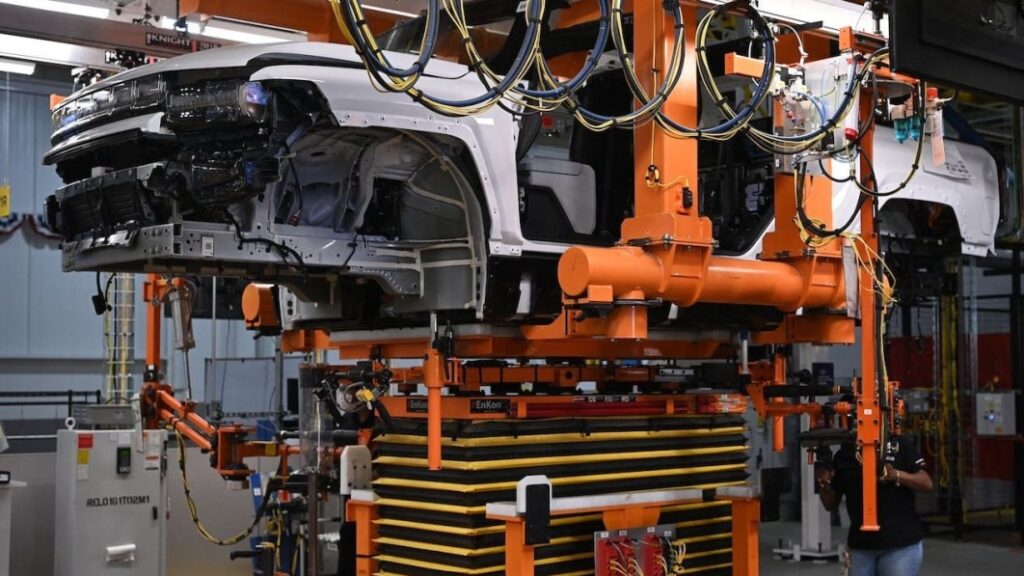
Automakers might need to copy
Tesla’s playbook for
battery sourcing. Here, a battery is installed in the
Hummer EV.
Mandel Ngan/Getty Images
Auto companies need EV battery supply more than ever, but the costs are adding up.
Prices and a push to use local materials have carmakers investing in in-house battery supply.
This move copies what Tesla has long been doing for years.
With electric car battery costs on the rise, auto companies are doing everything they can to make their EV offerings more affordable for the masses in the coming years.
Making that happen may require forgetting much of what they’ve learned about supply chains over a century, and replacing it with a few pages from Tesla’s playbook.
Automakers have been trying to evade today’s EV woes by exploring different kinds of batteries to slash their dependence on the in-demand materials found in traditional lithium-ion setups. They’ve also been ramping up battery recycling efforts and working to return lithium, nickel, cobalt and more into the supply chain.
These solutions come with challenges in terms of timing and expense, at least in the near term. That means car companies are seeking an alternative and racing to secure their battery supply in the US.
That means making investments in battery material sourcing, battery production, and more, to reduce the global supply disruptions the industry saw from the pandemic.
“Almost all the major companies are investing in that for that very reason: to vertically integrate more and get more control of their supply chain,” said Peter Maithel, auto industry principal analyst at Infor.
Volkswagen is building a battery cell factory at its Salzgitter site for its planned large-scale production of the Group’s own battery cells.
Julian Stratenschulte/picture alliance via Getty Images
What’s the rush?
In the past, car companies have expanded their supply chains across the globe, relying on slews of suppliers for each component of a car. Some of their key parts might come from the US, while others might come from Europe or Asia.
Historically, the breadth of those supply chains has reduced potential bottlenecks. But the pandemic — and other disruptions, like natural disasters — shed a light on just how vulnerable that can also make auto companies. If an auto parts plant across the world sees even a minor disruption, that could bring down a manufacturing line for days or weeks at a time.
The dawn of EVs, and the nuances in sourcing for these cars, brings those concerns and more to the forefront of automaker to-do lists. The US in particular has relied on foreign sources for battery supplies, components, and processing. China, meanwhile, has had a headstart in terms of sitting on the raw materials necessary to power EVs and controlling production of much of the world’s battery cells, packs, and more.
But whether it’s an unforeseen disruption like COVID-19 or a geopolitical issue, that leaves companies pretty vulnerable — and has encouraged them to bring manufacturing closer to home. There’s been a general push to get away from that world-wide supply chain model anyway, driven by this summer’s climate law.
“We’ve just seen an unprecedented amount of announcements, joint development agreements, early supply contracts from the automakers with battery materials providers, with battery manufacturers,” said Matt Sculnick, executive director of Nomura GreenTech’s advanced transportation team, “in a collaborative way that I don’t think we’ve really seen.”
Rivian manufactures its EVs in Illinois.
Rivian
Good news for EV adopters — eventually
It’s called vertical integration — and it’s something Tesla has long been known for.
“Tesla is always the groundbreaker here, going directly to the source, going directly to the mines and negotiating supply contracts with the mines,” said Alvarez & Marsal managing director Tony Lynch.
It’s given Tesla an advantage in terms of having visibility into production, while GM and Ford and others scramble to get in on US mining deals and manufacturing.
It’s complicated and time-consuming, but may ultimately be the best way car companies can get closer to lowering the cost of new EVs. Those sat at about $55,001 in April, according to Kelley Blue Book — about $10,000 less than a few months ago — with new gas-powered cars averaging $48,281 that same period, or roughly the same as last year.
More supply in general, but especially in the US, combined with more EV volumes, will drive that down.