Why are other automakers chasing Tesla's 'Gigacasting'?
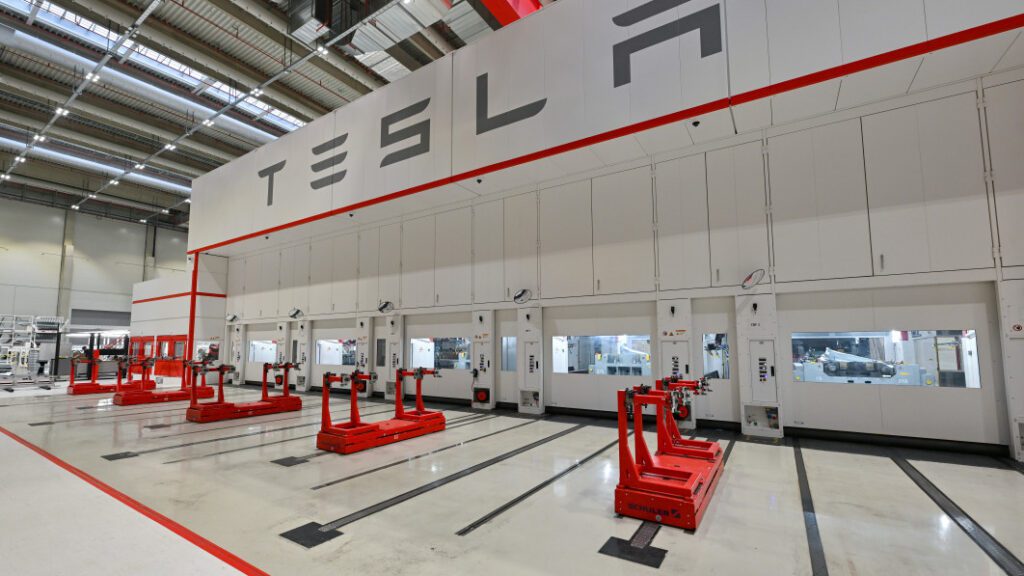
Toyota Motor has said it will adopt a technology Tesla pioneered known as “Gigacasting” as part of a strategy by the Japanese automaker to improve the performance – and lower the cost – of future electric vehicles (EVs).
Toyota is not alone in following Tesla’s breakthrough.
Here’s a look at Gigacasting and how the innovation is forcing automakers to scramble to match Tesla:
What is gigacasting?
The Giga Press is an aluminum die-casting machine adopted by Tesla at its factories in the U.S., China and Germany. The house-sized machines are able to produce aluminum parts far bigger than anything used before in auto manufacturing.
The “giga” in the name is a nod to Tesla’s convention of calling its plants “Gigafactories”. Other automakers have taken to calling them “megapresses,” which also can refer to smaller but still massive machines.
In operation, the press takes in a shot of molten aluminum of 80 kilograms (176 pounds) or more into a mould where it is formed into a part, released and then quickly cooled.
Tesla has developed an aluminum alloy that also allows it to skip the heat treating traditionally used to increase the strength of the cast part.
What’s the payoff?
Typically more than a hundred individually stamped metal parts have been welded together to make a car body.
Fewer parts, lower costs and a simplified production line have contributed to Tesla’s industry-leading per-car profitability, analysts have said.
For Tesla, the use of a single component in the rear of the Model Y — its best-selling model — allowed it to cut related costs by 40%, the company has said.
In the Model 3, by using a single piece from the front and rear of the vehicle, Tesla was able to remove 600 robots from assembly, Elon Musk has said.
It can also cut a vehicle’s weight — an important consideration for EVs where the battery pack alone can weigh more than 1,500 pounds. And it has the potential to reduce waste and greenhouse emissions from a plant.
Toyota said it expected that using aluminum die-casting would eliminate dozens of sheetmetal parts from assembly and reduce waste.
Who makes these machines?
Tesla sources its presses from Italy-based IDRA, which has been a unit of China’s LK Industries since 2008.
Competitors of IDRA and LK include Buhler Group in Europe, Ube and Shibaura Machine in Japan, and Yizumi and Haitian in China.
The global aluminum die-casting market was worth almost $73 billion last year and is projected to top $126 billion by 2032, showed an AlixPartners analysis.
Who’s chasing it?
In addition to Toyota, General Motors, Hyundai Motor and affiliates of China’s Geely — Volvo Cars, Polestar and Zeekr — are using the technology or planning for it.
Zeekr has started using massive aluminum die casts for a multi-purpose van it makes for sale in China and has said it will introduce the technology for other models.
Volvo said last year it would invest more than $900 million to upgrade its plant near Gothenburg, Sweden, to include megapress technology.
What’s the catch?
Cost is one.
Tesla records most of its sales with just two models: the Model 3 and Model Y. High sales volume on just two platforms make it easier to justify the investment in new production technology. Other EV startups also have that advantage.
For legacy automakers with more complicated product lineups and factory machinery that is already amortized, the decision to invest tens of millions of dollars in new casting technology can be a harder call, analysts have said.
Cars with body sections cast into single pieces could also be harder or more expensive to repair after an accident. That could add to the cost of operation for EVs.
Already insurance companies are totaling Teslas and other EVs with low mileage if they have damaged batteries because there is often no way to repair even slightly damaged battery packs.