With persistent rain forecast, see HSB's guide 'Water damage on construction sites'
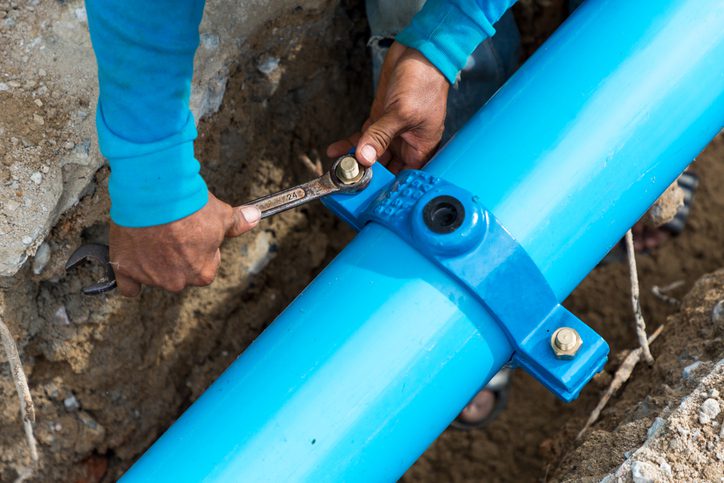
Authored by HSB
Water damage is the second most frequent cause of loss during building projects, representing a large percentage of Construction All Risk (CAR) claims.
Water damage occurs in large and small projects alike and it can bring an entire construction project to a halt. From rain entering a structure through openings in the roof and unfinished windows, to plumbing systems that leak when tested, to flood waters that appear when snow melts, water damage is a significant cause of loss to buildings under construction
It can ruin interiors, spur the growth of mould and damage electrical equipment. It can result in construction delays as affected areas dry out and damaged materials are discarded and replaced. It can reduce profit and add significant delays to completion schedules through clean up and replacement times. The contractor will pay at least some of the costs out of their own pocket in the form of deductibles, debris removal costs that exceed the insurance coverage, and income lost due to delays even when insurance applies to the loss.
Preventing water damage claims adds to a contractor‘s bottom line. With a focus on reducing construction defects, most water losses are preventable. Preventing water damage is critical to a construction business owner, even if insurance is in place. Losses can include property damage, debris removal, re-work and delay costs, not to mention the damage to reputation. It generally costs very little to prevent water damage and primarily requires a focus on quality, planning and testing throughout the construction process.
Water damage occurs from water entering the building envelope or from internal building releases.
These releases are most costly when water sensitive equipment has been installed prior to the water release or intrusion, or after interior fit-out has been completed.
As well as direct costs of clean up, repair, replacement and dealing with items such as mould, there can be long delays in restarting construction.
Prevention
Project Management and the Water Damage Prevention Plan
Using good risk management practices that can be implemented as part of the construction plan, most water damage losses can be prevented with very little impact on the budget. Prevention should be considered at all phases of construction:
Pre-constructionDuring active constructionProject close out
Usually there are items that are addressed at high level as well as measures that are addressed best at site level. Good project management to design out potential sources of water damage coupled with a job-specific water damage prevention plan should both be part of any project.
Water damage sources
Internal building sources
Plumbing systemMechanical systemDrainage systemFire Protection system
External water sources
RainRoofs and roof drainsDoor & window openings/roof openingsGroundwater
Construction defects
Door, window and wall deficienciesRoof, gutter and window flashingsWaterproofing and damp proofingCracks and separations in waterproofing structuresFlooded excavations
Pre-construction
During the first phase, pre-construction, it is necessary to design a formal Quality Assurance/Quality Control (QA/QC) plan. Following this plan, additional peer review of the construction drawings and specifications should be performed before executing a project. Evaluate the contract documents for areas of water infiltration susceptibility, and consider the drainage of water away from the structure and planned excavations.
Design team should engineer out sources of water damage. For example:
Combined service risersConcealed pipework routesPositioning of water tanksPorous risersPlumbing systems with a high vulnerability to failure (eg plastic push-fit and glue systems)
The design should allow for:
Additional isolation valvesRiser upstandsFull and easy access to pipesTemporary drainage points
A comprehensive risk assessment should be undertaken that considers, amongst other items:
Loss historyOccupancySusceptibility to water damageMitigation featuresSafeguards
A peer review of all construction drawings should be completed before construction work commences. This should include a review of:
MethodsMaterialsCode complianceCompatibility with local conditionsSubcontractor standardsQuality controlWater drainage and site conditions
Before starting construction, it is also important that the contractor evaluate the inter-relationship of specified materials and building systems.
If an area of weakness is identified, clarification should be sought from the engineer in the form of a Request for Information (RFI). Schedule the installation and testing of piping systems, such as hydronic systems, as early as possible in the project. This will minimise damage, as the majority of finished work will not have been started. Backup power and pumping systems must also be considered to prevent dewatering issues during construction.
Water leak detection units
One of the most effective ways of reducing damage from water leaks in projects is to use a water leak detection unit. These are installed into the water mains supply and can be installed for the building or on a floor by floor or even room by room basis.
The unit works by monitoring the volume of water in litres used in any selected time periods, for example per half hour or per day. The user sets the maximum volume of water allowed for each time period and if the maximum volume of water is exceeded in a given period, for example when a water pipe bursts in the night, the water supply will automatically be shut off, protecting the building.
During active construction
During construction, a designated site representative with responsibilities for adherence to the quality plan should be in place. This designated site representative will be responsible for development and implementation of the quality plan and for its continual updates and improvements throughout the project. It is critical that subcontractors work be included in the QA/QC plan and that a “no defects“ policy is communicated to all subcontractors. This policy should be reinforced through inspections, documentation and regular meetings. Specifically review the coordination of subcontractors‘ scopes to ensure that no waterproofing details have been overlooked.
Dedicate a team to focus on water preventionTrack and monitor problems and repairsTrain employees and subcontractors about quality standardsEstablish a weekly check list to mitigate water issues, and close out all issues weeklyMock-up all critical waterproofing systems prior to construction and discuss critical building system details and inspection concernsUndertake frequent testing, and if a problem is found, address it immediatelyNever pay for work with waterproofing issues unresolved
The building‘s structure should be fully enclosed, with all windows, doors, walls and roofs complete prior to the installation of finishes (never allow scheduling pressures to modify this sequence). Once the roof is installed on your construction project, conduct extensive water tightness testing. After this testing has been performed, maintain a roof free of debris during construction, and ensure regular inspections are carried out to identify any potential problems. If there are any problems, quickly address and repair them before damage occurs.
In addition to water-tightness testing, make sure that fire protection systems are hydrostatically tested per requirements of the most recent edition of NFPA 13 “Standard for the Installation of Sprinkler Systems,“ and monitor for leakage during testing. In addition, air pressurisation testing of all piping systems should be performed prior to charging with water, even if the system passed a hydrostatic test previously. Always charge piping systems by zone and not with all valves open. This will minimise the chances of a large unnoticed water release. When charging piping, establish personnel whose sole responsibility is monitoring piping systems for at least the first 24 hours.
Take action during or after an emergency
To ensure that prompt and proper action is taken during an emergency, a formal Severe Weather Disaster Plan should be developed. This should:
Describe duties and responsibilities in case of a major leakDescribe duties and responsibilities in case of severe weather eventsInclude all possible scenarios and a specific course of action for eachDelegate one person to be in charge that will take control during an emergency
If structural failures occur, such as cracks or fissures, as a result of settlement or displacement due to major leaks/water damage, contact the structural and geotechnical engineer for advice immediately, rather than making aesthetic corrections to the structure. During construction, prevent the accumulations of snow and ice to prevent structural failures and water infiltration, especially when the structural system is not fully established. Provide security personnel with a list of who to call 24/7 in the event of an after-hours water release or emergency.
Post construction close out
During the project close period, it is important to maintain a dedicated check-list team, and reserve them for check-list related repairs. This ensures that adequate resources exist to close the project properly. Address the check-list items on a weekly basis to ensure that only a week‘s worth of check-list items remain at the end of the construction period.
Maintain a team that can respond quickly to warranty issues, and resolve all water issues as soon as possible and no later than 48 hours. Take all “good faith“ efforts to prevent further damage if water is discovered. Check list should take account of:
Unsecured building openings
Door and window openingsRoof openings building envelopeDoor, window and exterior wall deficienciesRoof, gutter and window flashingsDamp-proofing and waterproofing
Water delivery or drainage system failure
Plumbing systemFire protection systemMechanical systemDrainage system
Site drainage problems
Improper drainage away from excavations and building structuresInadequate retention ponds
Subsurface drainage problems
Foundation and structural element problems
Cracks/fissures in waterproofing structuresSeparation of building envelope elementsFlooded/undermined excavationsExcessive/premature loading
Material storage problems
Water sensitive equipment installed improperlyFailed just-in-time delivery resulting in improper storage
Construction insurance solutions and inspection services
We have a comprehensive range of construction insurance products covering all aspects of projects across the UK and Ireland.
Our engineering inspection services also help customers to maintain workplace equipment safety, optimise the efficiency of a vast range of plant and equipment, and comply with applicable health and safety legislation.
HSB Construction Insurance
HSB Inspection Services