Loss prevention during energy curtailment
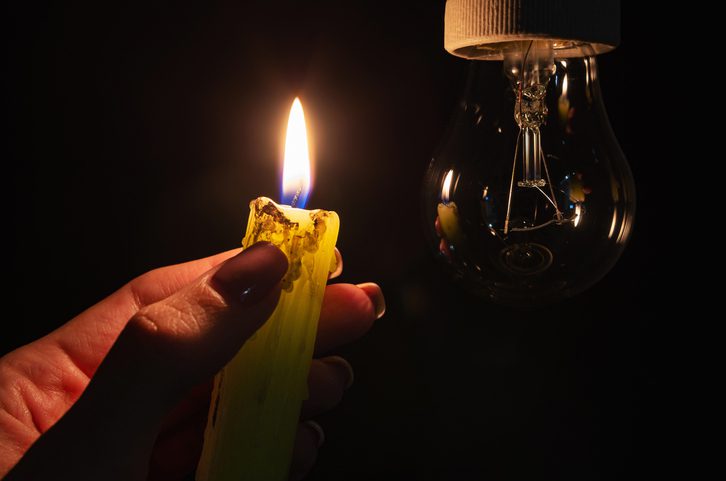
By AXA XL Technical Department Manager Karim Karzazi and Property Center of Expertise Leader John Frank
Companies operating primarily or exclusively in developed countries usually have little experience with situations where disruptions in the energy supply require operations to be shut down or curtailed. Moreover, in those rare instances when the power supply is interrupted—often due to severe storms or mechanical breakdowns—the situation is typically resolved within a few hours or, at most, days.
This time could be different. Given the current geopolitical situation, companies operating in some European Union countries could face energy curtailments lasting several weeks, if not longer. Although this is still only speculation—and the scope and length of such disruptions are impossible to predict—the likelihood of a company’s energy supply being cut off or curtailed isn’t small. Thus, companies operating in the EU should assess the ramifications of being without power for an extended period and consider their options for limiting the impacts.
This article outlines some potential implications and mitigating measures. This guidance isn’t meant to cover all possibilities and contingencies—that isn’t feasible given companies’ diverse operations and circumstances—but rather to help stimulate discussions, analyses and the refinement of contingency plans designed to minimize the impacts. Also, the suggestions outlined below assume that the energy supply is suspended for at least one week during subfreezing temperatures and that there could be more than one curtailment event.
Provide alternative energy supplies
This is obvious but bears repeating: First and foremost, alternative energy supplies should be secured.
When assessing their needs and the options for meeting them, companies should consider three issues:
Will the local authorities allow some energy consumption, and if so, when and at what levels? Since so many other factors hinge on this, companies should immediately engage with their energy suppliers to ensure they are promptly informed of scheduled curtailments.How much energy will critical processes and equipment need?What buildings or equipment could be disconnected from the energy supply for load-shedding purposes, and what are the likely consequences of doing so?
When deciding what non-essential buildings or operations can be disconnected, don’t overlook safety and protection equipment that needs power or heat during emergencies. For example, a non-priority building that otherwise would be shut off but houses a sump pump used to prevent flooding during periods of heavy precipitation. Or the elements of the fire protection systems that require electricity and, in some cases, adequate heat to function properly. (More on this below.)
Also, the emergency energy supply should be tested beforehand to ensure it can handle the expected load. If such a test isn’t possible, the facility should assume a worst-case scenario and prepare for a shutdown.
Protect critical machinery
While many machines/processes can operate without building heat or gas, they still need electricity. Thus, a total shutdown, possibly including fire protection, may be required if gas and electricity are lost.
Industries with susceptible processes—for example, aluminum smelting, molten glass, blast furnaces and cement kilns—have well-established procedures for re-starting operations after a stoppage, whether planned or unexpected. Those procedures should be reviewed, and a tabletop or other practice run conducted. In less susceptible industries, guidance from the manufacturer should be sought.
If allowed by government officials, minimal power to critical machinery should be maintained. Some examples include:
Rotary kilns should be kept on minimal rotation speed to prevent damage to the equipment.Chemical operations are vulnerable to loss of cooling, stirring or inhibitors. A review of chemical process safety analyses can show what parts of the process are vulnerable and what steps are needed to maintain critical operations or to allow for a safe and stable shutdown.Loss of refrigeration and the resulting spoilage doesn’t affect just large freezers. Small walk-in or home-sized units could hold critical laboratory samples, high-value pharmaceutical products, etiological agents, and the like.Turbines need power to ensure adequate lubricating oil flow, especially during the “coast down” period. This could take a full day to accomplish without damage to the equipment.The loss of off-site data servers could impact almost every aspect of a facility’s operations. Thus, companies should assess the provisions their technology partners have taken to ensure uninterrupted coverage in the event local energy supplies are curtailed.
Secure the alarm systems
All alarm systems—whether for fires, intrusion or process safety—have backup batteries. However, the batteries aren’t intended for extended curtailments. Depending on the system, they are usually set for 12-72 hours, rarely more.
Consider replacing older batteries and adding additional batteries to extend the duration.
Also, if the curtailment lasts for at least two weeks, the performance of the alarm systems shouldn’t be assumed, and guard patrols should be deployed for detection and notification.
Minimize fire risk
Although fire risk is less in partially or wholly shut buildings, keeping the fire protection systems in service should be a priority. In particular, ensure that the sprinkler systems and associated pumps will perform adequately in unheated buildings and have sufficient power from batteries, backup generators or other sources.
Loss of heat: As energy curtailments are most likely during the winter, measures should be taken to ensure the sprinkler system doesn’t freeze and cause the pipes to break. These include:Seal known cold air incursion points.Aim to maintain a temperature above 4.4° C (40° F) since wet pipe sprinkler systems can be left in service above this level.In areas colder than the average indoor temperature, inexpensive battery-powered thermometers with remote monitoring should be installed.Loss of power in systems with diesel-driven fire pumps: Diesel pump engines need power for long-term battery charging, especially in cold weather. Likewise, the engine block heater is electrically powered; if it fails, the engine eventually won’t start. The upshot: If the batteries die and the pumps can’t start, the sprinklers won’t function. Consider replacing older batteries with the latest top-quality batteries to ensure they will perform if needed.
Alternatively, if diesel fuel is available, short (e.g., 10-minute) pump runs will help keep the batteries charged. And if a controller doesn’t function, plant personnel should know how to start the pump manually.
Loss of power in systems with electrical-driven fire pumps: Obviously, electric fire pumps can’t run without power, so backup diesel generators should be available. In that case, the diesel fire pump principles outlined above apply.Avoiding corrosion risk: If energy curtailments happen frequently, the fire pumps may need to be shut down and drained. However, draining and refilling the systems can increase corrosion, especially if done more than once. In this case, installing special corrosion or freeze-protected systems should be considered. Also, corrosion inspections should be conducted after conditions have returned to normal.Avoiding uncontrolled fires: Although, as noted, fire risk is less during periods of energy curtailment, any fires that occur will be much more difficult to control. To minimize these risks, the following steps should be taken:No hot work operations should be undertaken when the sprinkler systems are shut down. (This also applies during normal operations.)Maintain constant vigilance by guards with immediate access to portable fire extinguishers.Invite the public fire brigade to tour the facility beforehand. This will increase the probability of successful manual firefighting. Also, consider hiring standby firefighters with contracted firefighting equipment.Report impairments through RSVP (Restore Shut Valves Promptly).If you are a client, we would recommend establishing the AXA XL WaterWorks procedure to manage any pipe breaks that do occur.
Secure adequate materials
Energy-intensive industries like aluminum and steel smelting, glass manufacturing or cement production will naturally be most severely impacted by any curtailments; companies in these sectors should thoroughly assess their options for limiting the consequences. At the same time, businesses that rely on materials from energy-intensive industries also should take appropriate precautions by, for example, stockpiling materials or identifying alternative suppliers. In other words, the disruptions caused by energy curtailments could quickly reverberate across the regional economy, including in countries where the supplies aren’t reduced.
Broadly relevant
Although this guidance was prepared in response to the current geopolitical situation, it also applies to, and was informed by, other instances in which the energy supply is or was curtailed for an extended period, e.g., following a severe storm or periods of civil unrest. As such, we hope this article helps companies better understand and prepare for the challenges associated with prolonged energy curtailments and that they may benefit from our suggestions in their ongoing contingency plans. While it isn’t possible to foresee all likely scenarios, there is no question that good planning improves an organization’s ability to respond to and recover from unexpected events. AXA XL’s Risk Consultants also stand ready to assist clients in these efforts.